Napake in okvare komponent so življenjsko dejstvo. Tiskana vezja so včasih dobavljena s proizvodnimi napakami, komponente so lahko spajkane nazaj ali v napačnem položaju, komponente pa se pokvarijo. Zaradi vseh teh možnih točk napake vezje deluje slabo ali pa sploh ne deluje.
Odpravljanje težav s PCB
Tiskana vezja ali PCB so množica izolatorjev in bakrenih sledi, ki povezujejo gosto zapakirane komponente v sodobno vezje. Odpravljanje težav s PCB-ji je pogosto izziv, pri čemer igrajo veliko vlogo dejavniki, kot so velikost, število plasti, analiza signala in vrste komponent.
Nekatere bolj zapletene plošče zahtevajo posebno opremo za pravilno odpravljanje težav. Vendar je večino težav mogoče odpraviti z osnovno elektronsko opremo za sledenje sledom, tokovom in signalom skozi vezje.
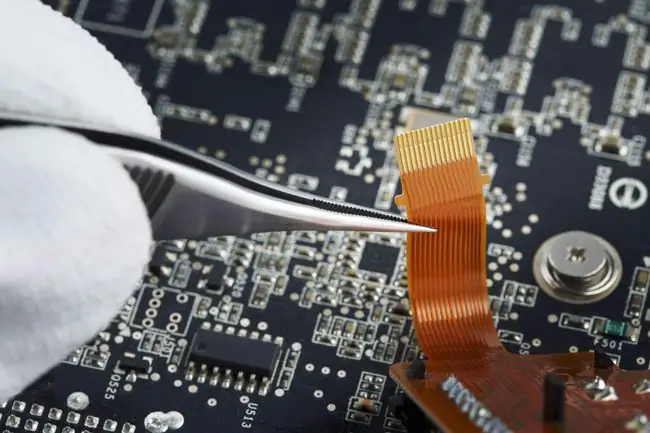
Spodnja vrstica
Za večino osnovnih težav s PCB potrebujete le nekaj orodij. Najbolj vsestransko orodje je multimeter. Odvisno od kompleksnosti tiskanega vezja in težave pa bodo morda potrebni tudi merilnik LCR, osciloskop, napajalnik in logični analizator, da se poglobimo v delovanje vezja.
Opravite vizualni pregled
Vizualni pregled tiskanih vezij odkrije bolj očitne težave, vključno s prekrivajočimi se sledmi, pregorelimi komponentami, znaki pregrevanja in manjkajočimi komponentami. Nekaterih zažganih komponent, poškodovanih zaradi premočnega toka, ni mogoče videti tako zlahka, vendar lahko povečan vizualni pregled ali vonj nakazujeta prisotnost poškodovane komponente. Izbočene komponente so še en dober pokazatelj težave, zlasti pri elektrolitskih kondenzatorjih.
Opravite fizični pregled
En korak naprej od vizualnega pregleda je fizični pregled z napajanjem vezja. Z dotikom površine tiskanega vezja in komponent na plošči lahko zaznate vroče točke brez uporabe drage termografske kamere. Ko zaznate vročo komponento, jo ohladite s stisnjenim zrakom v posodi, da preizkusite delovanje vezja s komponento pri nižjih temperaturah.
Ta tehnika je potencialno nevarna in jo je treba uporabljati le v nizkonapetostnih tokokrogih z ustreznimi varnostnimi ukrepi.
Ko se dotaknete električnega tokokroga, upoštevajte nekaj varnostnih ukrepov. Prepričajte se, da je le ena roka kadar koli v stiku z vezjem, da preprečite, da bi potencialno usoden električni udar potoval čez vaše srce. Če je mogoče, je pri delu na tokokrogih pod napetostjo dobro držati eno roko v žepu, da preprečite takšne udarce. Prepričajte se, da so vse potencialne tokovne poti do tal, kot so vaše noge ali neuporovni ozemljitveni trak, odklopljene, da zmanjšate nevarnost udarcev.
Dotikanje različnih delov vezja prav tako spremeni impedanco vezja, kar lahko spremeni obnašanje sistema in tako identificira mesta v vezju, ki potrebujejo dodatno kapacitivnost za pravilno delovanje.
Izvajanje testiranja diskretnih komponent
Testiranje vsake posamezne komponente je pogosto najučinkovitejša tehnika za odpravljanje težav s PCB. Preizkusite vsak upor, kondenzator, diodo, tranzistor, induktor, MOSFET, LED in ločene aktivne komponente z multimetrom ali merilnikom LCR. Če so komponente registrirane manj kot ali enake navedeni vrednosti komponente, so komponente običajno dobre. Če je vrednost komponente višja, je to znak, da je komponenta slaba ali pa je spajkalni spoj slab.
Preverite diode in tranzistorje z uporabo načina testiranja diod na multimetru. Spoji baza-emiter in baza-kolektor tranzistorja bi se morali obnašati kot diskretne diode in prevajati samo v eno smer z enakim padcem napetosti. Nodalna analiza je še ena možnost, ki omogoča testiranje komponent brez napajanja z napajanjem posamezne komponente in merjenjem njenega odziva napetosti proti toku (V/I).
testiranje ICs
Najzahtevnejše komponente za preverjanje so IC-ji. Večino je mogoče zlahka prepoznati po oznakah, mnoge pa je mogoče operativno preizkusiti z uporabo osciloskopov in logičnih analizatorjev. Vendar pa lahko število posebnih IC-jev v različnih konfiguracijah in zasnovah tiskanih vezij naredi testiranje zahtevno. Primerjava obnašanja vezja z znanim dobrim vezjem je pogosto uporabna tehnika in bi morala pomagati, da nenormalno vedenje izstopa.